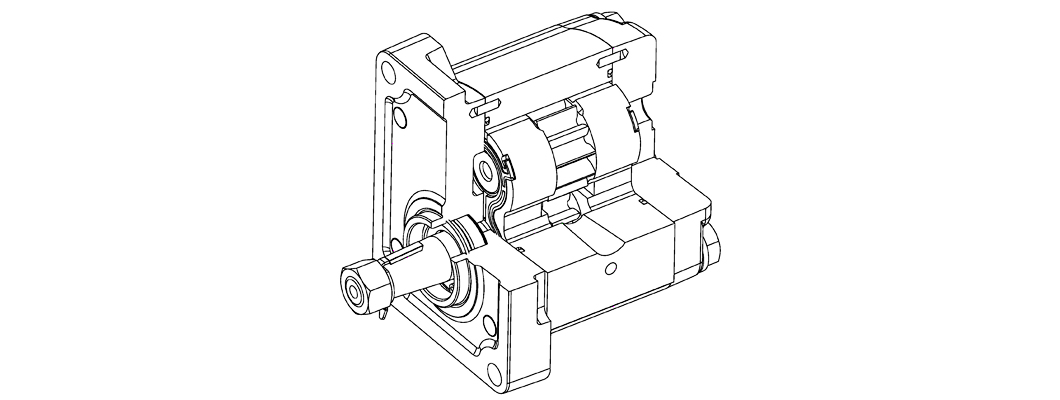
Tasarım Konfigürasyonu Olarak Hidrolik Dişli Motorlar
Hidrolik motorlar, hidrolik enerjiyi mekanik enerjiye dönüştürmek için kullanılan motorlardır. Farklı projelere cevap vermek için kullanılan hidrolik motorlar, bu projelere cevap verebilmek için pek çok farklı tasarımda üretilir. Bu tasarımlardan biri de hidrolik dişli motorlardır.
Hidrolik Dişli Motor Nedir?
Hidrolik dişli motorlar, hidrolik akış ve basıncı mil yoluyla açısal yer değiştirmeye ve torka dönüştürür. Bu motorlar, genel kullanımlara daha uygundur.
Kullanım alanlarına göre çift veya tek yönlü olarak tedarik edilebilen hidrolik dişli motorlar, uygulama şartlarına bağlı olarak alüminyum veya döküm gövdeli olarak tercih edilir. Radyal yükleri karşılayabilecek şekilde tasarım seçenekleri mevcuttur. Ayrıca uygulama ihtiyaçlarını karşılayabilecek basınç emniyet valfli, anti kavitasyon valfli, hız sensörlü olarak alternatifleri de bulunur.
Tasarım Konfigürasyonu Olarak Hidrolik Dişli Motorların Tercih Edilmesi
Hidrolik dişli motorlar, mümkün olan en az sürtünme ile çalışarak daha yüksek tork üretilmesini sağlamak amacıyla tasarlanmıştır.
Dişli motorların avantajları şunlardır:
- Küçük boyutlara sahip ve hafiftir.
- Düşük maliyetlidir.
- Geniş hız aralığına adapte olur.
- Geniş sıcaklık aralığında çalışabilir.
- Geniş viskozite aralığı için uyumludur.
- Darbelere karşı dayanıklıdır.
Kullanılan hidrolik yağın kirlilik seviyesinin NAS 9 değerinden
yüksek olması motorun ömrünü olumsuz etkileyen bir unsurdur. Parçalar üzerinde aşınmaya
neden olarak motor veriminin düşmesine neden olur.
Herhangi bir sorunla karşılaşmadan önce hidrolik dişli motorlarda bulunan dişliler, kullanılamaz hâle gelene kadar ana burçları veya gövdeyi kademeli olarak aşındırır. Verimliliği kademeli olarak düşürerek, yıkıcı sorunla karşılaşmadan önce dişli motorun değiştirilmesi gerektiğinin işaretini vermiş olur. Böylece makine durmadan ve beraberinde proje sekteye uğramadan önce önlem alınabilir.
Hidrolik Dişli Motor Seçimi Yaparken Dikkat Edilmesi Gerekenler
Hidrolik dişi motor seçimi yaparken kullanılacak proje ve makinenin özellikleri göz önünde bulundurulmalıdır. Bir makinenin verimliliğini doğru şekilde değerlendirmemek maliyetli sonuçlara neden olur. Enerji tasarrufunun önem kazandığı günümüzde, verimli dişli motorlar seçilerek enerji tüketiminin minimum düzeyde tutulması maliyetleri azaltacaktır.
Tüm bu ihtiyaçlara göre makinenin sistem gereksinimi, makineden beklenen performans ve kullanım alanı hidrolik dişli motor seçimini belirler.
Makine ve çalışma koşulları gereksinimlerini belirledikten
sonra, hidrolik dişli motor seçimi yapmadan önce birkaç önemli faktörü göz
önünde bulundurmak gerekir:
- Gerekli olan çıkış torku (Nm)
- Sistemin minimum ve maksimum basıncı (bar)
- Çalışma sıcaklık aralığı (C)
- Maksimum çalışma hızı (rpm)
- Gerekli olan iletim hacmi (cc)
Bağlantı flanşı, şaft ve giriş-çıkış port ölçüleri
Hidrolik dişli motorlar ve hidrolik dişli pompalar, hidrolik makinelerin çalışması için birbirlerini tamamlayan mekanizmalardır. Tasarım farklılıkları sebebiyle çalışma prensipleri de farklıdır.
Hidrolik Dişli Pompa ile Hidrolik Dişli Motor Arasındaki Fark Nedir?
Hidrolik motorlar, hidrolik enerjiyi mekanik enerjiye dönüştürür.
Pompalar ise mekanik enerjiyi hidrolik enerjiye dönüştürür.
İkisi farklı işleme toleransları ile üretilir ve farklı şekilde test edilir. Bu farklılıklar olsa da hidrolik dişli motor ve pompaların tek ve çift yönlü olarak iki dönüş yönü seçeneği mevcuttur.
Leave a Comment