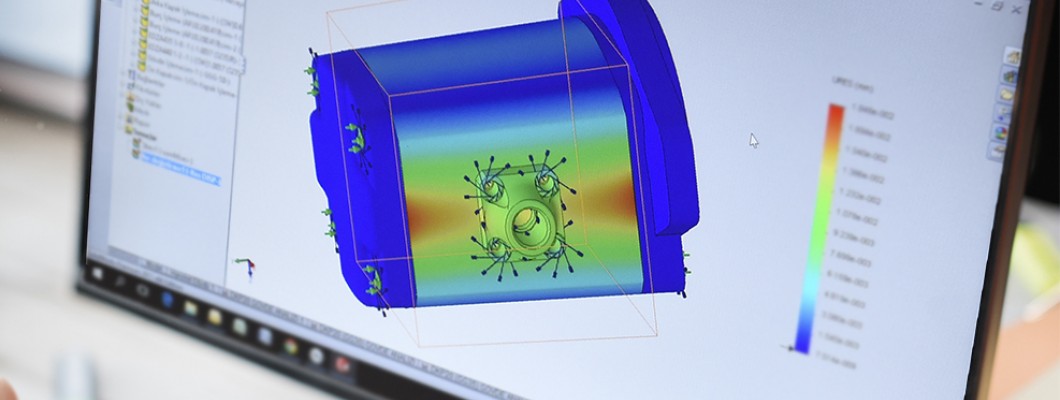
Hidrolik Dişli Pompa Seçimini Belirleyen 4 Tasarım Özelliği
Hidrolik sistemler ile çalışan ekipmanlarda hidrolik yapılardan en yaygın kullanılanlardan biri de hidrolik dişli pompalardır. Bu pompaların az sayıda hareketli parçaya sahip olması, bakımlarının kolay olmasını sağlar. Ayrıca, toza ve kirliliğe daha toleranslı olmaları ve düşük maliyetli olmaları da tercih edilmelerini etkileyen faktörler arasında yer alır. Basit yapıları, yüksek emiş seviyeleri ve verimlilikleri de bu pompaları avantajlı kılar.
Hidrolik dişli pompaların kullanım alanları nelerdir?
Hidrolik dişli pompaların üretim aşamasında çeşitli tasarım ilkeleri ve konfigürasyonlar uygulanır. Yaygın olarak kaldırma, indirme, açma, kapatma veya döndürme gibi farklı gereksinimlerin olduğu, güvenli ve uzun ömürlü olması beklenen her proje ve sektörde kullanılabilir.
Hidrolik dişli pompa seçimi nasıl yapılır?
Hidrolik dişli pompa seçiminde pek çok kriteri göz önünde bulundurmak gerekir. Çalışma koşulları ve yapılacak işin gerektirdiği ihtiyaçlara göre üretilen farklı tiplerdeki bu pompaların seçiminde üretici firmanın tavsiyeleri de dikkate alınmalıdır. Seçim yaparken göz önünde bulundurulması gereken unsurlardan bazıları aşağıdaki gibidir:
· İstenilen basınç aralığı
· İhtiyaç duyulan devir sayısı
· Çalışma sıcaklıkları
· Beklenen gürültü seviyesi
· Kontrol tipi
· Bakım imkânları
· Maliyet
· Yağ kirliliğine karşı hassasiyet
Bu maddeler göz önünde bulundurularak hidrolik dişli pompa seçimine karar verilmelidir.
Kullanım Alanlarına Göre Hidrolik Dişli Pompa Seçimi
1. Gövde Tipi
Hidrolik dişli pompalar genellikle alüminyum ve döküm gövdeli olarak üretilirler.
- Alüminyum Gövdeli Dişli Pompalar
Gövdesi alüminyum olan dişli pompalardır. Geniş sıcaklık ve basınç koşullarında bile uzun ömürlü ve dayanıklı performansları sayesinde farklı endüstriyel ve tarım uygulamalarında yaygın olarak kullanılır. Sağlam ve güvenilir özellikleri ile geniş uygulama yelpazesine sahiptir.
- Döküm Gövdeli Dişli Pompalar
Gövdesi dökme demir olan dişli pompalardır. Döküm gövdeli dişli pompalar daha ağır basınç şartları için tasarlanmıştır. Yüksek çalışma basınçlarında üstün performans ve verimlilik ile çalışırlar. Mobil ve endüstriyel alanlarda özellikle malzeme elleçleme ve iş makineleri gibi ağır hizmet uygulamalarında kullanılırlar.
Hidrolik dişli pompalarda ihtiyaç duyulan kapak tipi, uygulama alanlarına göre farklılık gösterir. Bu nedenle bu pompalar kullanım yeri ve ihtiyaca göre farklı kapak tiplerinde tasarlanır ve üretilir. Doğru kapak seçimi için kullanılacağı ekipmanı tanımak ve kullanım ihtiyaçlarını bilmek gerekir.
2. İletim Hacmi
Hidrolik dişli pompalar, iletim hacimlerine göre farklı gruplara ayrılabilir. Bu pompaların her dönüşte ilettiği yağ kapasitesi, seçimi belirleyen önemli bir faktördür. Kullanılacak projeye göre iletim hacmi belirlenmelidir. Büyük projelerde yüksek iletim hacmine ihtiyaç duyulur.
3. Şaft Tipi
Şaft tipi, hidrolik dişli pompanın kullanım alanına göre farklılık gösterir. Makinenin ihtiyaçları göz önünde bulundurularak, gerekiyorsa, standardın dışında şaft seçimi yapılmalıdır. Özel durumlar için farklı tiplerdeki şaftların, farklı kapak tipleri ile kombinasyonu yapılabilir.
4. Gövde Delik Tipi (Bağlantı Tipi)
Pompanın dizaynını etkileyen bir diğer unsur da gövde delip tipidir. Hidrolik yağın düşük basınçla emilip yüksek basınçla çıkmasını sağlayarak sistemlerin hareketine yardımcı olur. Kullanım alanı ve istenilen basınç miktarına bağlı olarak gövde delik tipleri değişkenlik gösterir.
Leave a Comment